ZF and Grohe implement Cradle to Cradle Certified®
Cradle to Cradle Certified® is considered a very ambitious form of circular economy. ZF, Grohe and Bang & Olufsen have taken this path and show how it can be walked - even for medium-sized companies.
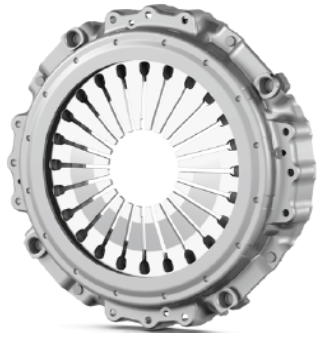
This is the English translation of an article originally featured in Industrie anzeiger (in German). Click here to read the original article.
Many companies today are asking themselves how they can make their products more sustainable. Be it from the perspective of climate protection, the circular economy or a broader sustainability approach. The principles of 'cradle to cradle' design, i.e. consistent circular thinking in product development, are finding increasing favor in industry. Automotive supplier ZF, sanitaryware manufacturer Grohe and consumer electronics specialist Bang & Olufsen use the design principle. But many medium-sized manufacturers are also already working with it.
The 'Cradle to Cradle' approach enables a holistic entry into sustainable product development. In addition, many have the advantage that products can be certified at different levels. The framework for this is provided by the Cradle to Cradle Products Innovation Institute. The non-profit and independent organization develops the Cradle to Cradle Certified product standard, which is used worldwide. In developing the criteria, the Institute attaches great importance to ensuring that they are science-based and developed in an open stakeholder dialog.
The automotive supplier ZF, for example, has developed clutch parts according to Cradle to Cradle Certified. The starting point was the simple question: Where do we actually stand in terms of sustainability? And behind this was the strategic perspective of how competition in the industry will develop in the future. Experience shows that customers are already increasingly asking for a smaller carbon footprint of products.
With Cradle to Cradle, ZF sets a benchmark
ZF was therefore concerned with a holistic approach that would also set a benchmark in the industry. The desire was to work with an internationally established system such as the 'Cradle to Cradle Certified' product standard - in line with the customer structure.
As part of its worldwide remanufacturing activities, ZF takes back used parts, remanufactures them, and puts them back on the market. At the Bielefeld location, one of the more than 20 ZF remanufacturing plants worldwide, approximately 40 to 50 tons of used clutch parts ("cores") arrive every day - of which between 80 and 95 % are remanufactured and returned to the market.
The basic idea of Cradle to Cradle is already partly incorporated in the business model here. The focus is not only on the production and selling price of the component. The money is earned over several cycles of use. Accordingly, one of the tasks of product developers is to precisely prepare and plan for these later uses.
Cradle to Cradle came into play to further optimize the clutch parts from a sustainability point of view and also to get impulses for other product developments. The ZF employees got started with the analysis and subsequent optimization of the products via the 'Cradle to Cradle Certified' framework.
The start: ZF analyzed product components
Based on this guide to action, they first broke down the product into its components and compiled a list of the materials used. In doing so, the product standard and the toxicological evaluation of substances gave them good orientation: Which materials are questionable or to be excluded from the perspective of sustainability and circular economy? Which alternatives should be considered? Where is potential for innovation?
ZF then took up the topic within its supply chain and sought suitable solutions in dialog with the respective manufacturers. With a good result. The material composition of the clutch parts could be further optimized from the perspective of a circular economy.
In parallel with the product, the focus shifted to production, with the questions that are well known in industry: What do energy generation and the CO2 footprint look like? Where is the potential for efficiency in the use of resources? How can wastewater and soil management be optimized? What do social manufacturing conditions look like? Well-positioned companies like ZF usually already have a well-founded data basis that helps them analyze and optimize their products according to Cradle to Cradle Certified.
Clutch parts remain in the circuit
It quickly became clear at ZF, how many environmental advantages remanufacturing has. The CO2 balance alone is significantly reduced due to the many life cycles of the clutch parts. These parts also do not end up as waste but remain in the cycle.
This is a basic idea that is likely to become increasingly important for the industry in the coming years. BMW, for example, recently unveiled its BMW I Vision Circular concept car. It shows what a car could look like in 2040 that is consistently designed according to the principles of the circular economy.
Against the backdrop of current industry developments, ZF's remanufacturing plant in Bielefeld has had its product portfolio certified almost entirely in accordance with the 'Cradle to Cradle Certified' Silver and Gold product standards, putting it in a leading position in the market.
Other industrial companies are also setting themselves on the development path to a circular economy, such as sanitary manufacturer Grohe. The brand is keen to help shape the paradigm shift in the sanitary and building industry. That's why Grohe has optimized several faucets and a shower rod set according to the 'Cradle to Cradle Certified' product standard. This involved recording and evaluating every ingredient in the products. Where necessary, Grohe made appropriate changes.
Grohe designs shower hoses according to Cradle to Cradle
One example is the "Cradle to Cradle Certified shower hoses". Previously, these hoses were made of multilayer PVC with plasticizers, but now they are made of high-purity silicone. The brand wants to use Cradle to Cradle to set itself clearly apart from all the requirements currently in force and change the market with product features that are not yet required but are ecologically sound and innovative.
This includes building on company networks within the industry, because only together can manufacturers be part of the solution to the currently pressing environmental problems. Only through cooperation can resource conservation and waste reduction be significantly advanced.
It is therefore not surprising that the manufacturer intends to further expand its Cradle to Cradle Certified range. In addition, Grohe is working on return processes for 'Cradle to Cradle Certified' products.
From Grohe's perspective, the certification process is challenging because it involves upstream manufacturing processes as well as internal production. However, according to the company, this work has been worthwhile, as the insights gained show what can be considered for future product developments from the outset and how resource consumption can be reduced.
Bang & Olufsen draws inspiration
Bang & Olufsen has introduced the first Cradle to Cradle Certified product in consumer electronics. The company consistently applied modular design principles in the development of a new loudspeaker. It also increased transparency in the supply chain and worked with suppliers to optimize the product's material composition. The aim is to drive sustainability within the company and close material loops.
The examples show that more and more companies are tackling more future-oriented product development. They are defining product quality and innovation more holistically. In addition to the traditional technical parameters, quality criteria such as recyclability and the carbon footprint are appearing as standard. A systemic approach in the respective value chain and industry is proving to be an important success factor for this.
The coveted Cradle to Cradle Certified Certification
The Cradle to Cradle Products Innovation Institute is dedicated to powering the circular economy through products and systems that have a positive impact on people and planet.
Through the Cradle to Cradle Certified® Products Program, the Institute sets the global standard for products that are safe, circular and responsibly made.
Cradle to Cradle Certified® is a comprehensive certification that assesses a product’s performance across five critical areas of sustainability:
Material Health: ensuring materials are safe for humans and the environment
Product Circularity: enabling a circular economy through regenerative products and process design
Clean Air & Climate Protection: protecting clean air, promoting renewable energy, and reducing harmful emissions
Water & Soil Stewardship: safeguarding clean water and healthy soils
Social Fairness: respecting human rights and contributing to a fair and equitable society
Cradle to Cradle Certified certification is awarded based upon four ascending levels of achievement from Bronze to Platinum. (Bronze, Silver, Gold, Platinum).